Applications and Case Studies
Zero emission cruise with automated centralheating system
On June 2nd, 2022, Havila Castor, owned by Havila Kystruten AS, made history in the Geirangerfjord in Norway – operating the first zero-emission cruise through the world heritage fjord.
In 2018, the Norwegian Parliament decided that cruise ships and ferries must sail emission-free in Norwegian World Heritage fjords as soon as technically possible, and no later than 2026. Havila Kystruten's managed to do this 4 year before the deadline with its newest addition to its fleet, “Havila Castor”.
The fleet of Havila Kystruten is built for the future and are the most environmentally friendly cruise ships operating along the Norwegian coast. With a battery pack of 6.1 Megawatt hours (MWh), the (at that time) world's largest battery pack on a passenger ship, the ships can sail up to 4 hours on pure battery power. In combination with liquefied natural gas (LNG), CO2 emissions are reduced by 30 % and NOX emissions by 90 % compared to similar vessels that use fossil fuel.
Critical to achieving the zero-emission cruise operation, is the automated central heating system, designed and delivered by Ulmatec Pyro AS (“Ulmatec Thermal Solutions”).
The main objective of the central heating system is to maximize utilization of the energy contained in the fuel (LNG) and ensure thermal energy balance onboard. Up to 56% of the energy content in the fuel is converted to surplus thermal energy during normal operation. After the fuel combustion process, the processes of heat recovery, heat generation, heat storage and heat distribution are managed and monitored by Ulmatec Pyro’s standard and configurable automation software.
Whilst recovering surplus thermal energy is not something new, the unique feature of Ulmatec Pyro’s systems is the functionality of automated flow distribution based on heating demand from the consuming systems. Such consuming systems can be HVAC, sanitary hot water, engine preheating, fuel preheating, heat to power systems or others.
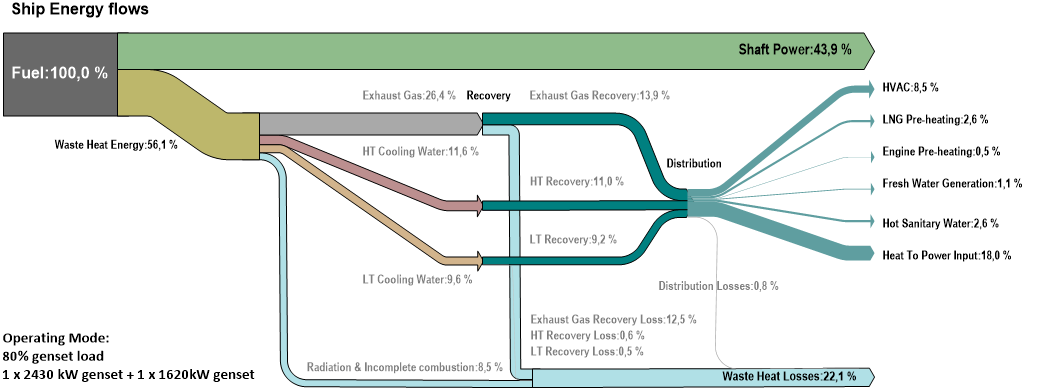
The illustration of the ships energy flow during normal (transit) operation highlights the achievements of the solution: Up to 78% of the energy content in the fuel is consumed and utilized, whereby 44% for diesel-electric power generation and 34% for thermal processes.
Together with HAV Design AS, the solution was developed by applying a very holistic thinking where electrical and thermal design disciplines worked closely together.
A key principle in heat design is that there is no reason to recover heat if there is no demand. As thermal energy degrades as it is converted, the most efficient use of thermal energy is direct use. During the design development, the joint project team was able to exploit the opportunities which lies in heating by hot water. Matching heat sources to heat sinks is an integral part of designing a waste energy system. In parallel, available technologies must be evaluated and selected in order to achieve technical, economic and environmental design objectives.
By throwing away old ideas, heating by hot water as a heating medium removed quite an amount of typical electrical load from the ship’s main switchboard – ultimately enabling an optimized power plant.
Heat recovery
Heat is recovered from exhaust gas flow, high (HT)- and low (LT) temperature cooling water from the four generator sets. Recovery is done by four economizers and heat exchangers. Recovered heat is circulated in two circular subsystems – a high and a low temperature system. The subsystems are connected and are able to exchange energy if required. Both subsystems are connected to the seawater cooling system.
Heat pumps are installed to upgrade seawater thermal energy and feed into the low temperature system when engine load is low or the ship is in port. This is a very efficient way of utilizing (shore) electricity to generate heat.
Thermal Storage
Quite often heat supply and demand are not synchronized. A typical example is port operation. With more stringent environmental regulations from ports, passenger ships face a challenge in the future of how to heat their ship during port stay. Shore power (“cold ironing”) is a viable option, but infrastructure and adoption by different ports is going slow. And, subsequently, what does the electrical energy cost?
A smarter option is to store the thermal energy whilst engines are running at high load and thereby conserve the fuel energy for later use. Havila Kystruten’s fleet is equipped with storage tanks for hot sanitary water, providing safe supply to its 640 passengers during port or zero-emission operation. In addition, the high temperature system integrates a high capacity buffer tank (“heat battery”) enabling a safe transition between operating modes and varying consumer heat demand.
Heat Distribution
Heat balance in the vessel is achieved through automatic flow regulation to consumer systems by Ulmatec Pyro’s proprietary Waste Energy Management System (Ulmatec WEMS™). The system is standardized, but configurable according to the specific vessel’s configuration of heat sinks and heat sources. This makes it a low cost and low complexity option for most vessel types. The core software module is identical whether it is a trawler or a cruise ship. For shipowners, this represents a huge benefit as the core module is constantly improved and upgraded with the addition of new features (e.g. remote assistance or energy monitoring and reporting).
For Havila Kystruten’s fleet, the Safe Return to Port (SRtP) regulations apply – meaning that the central heating system is designed as redundant (“two-split”). This is a critical feature, as engine cooling (and general heating) can persist after an incident.
Energy flow regulation is done by flow control units (FCU) in different locations. The FCU’s regulate the energy flow to consuming systems by temperature logging and valve control. In its own sense this data mining can become a source of further energy optimization for Havila Kystruten, as analysis of these data can provide insights into actual heat supply and consumption demand during various scenarios (e.g. seasonal). These insights can result in further tuning of the system, increasing energy efficiency further.
Circulation is achieved by 4 pump skids, greatly reducing the need for dedicated circulation pumps to selected consumer systems.
As a spinoff from the project, Ulmatec Pyro is now able to offer a central operating system (GUI), enabling overall control and monitoring capability from one central location (e.g Engine Control Room). The solution can be retrofitted to existing installations of Ulmatec WEMS™.
Heat to Power
Havila Kystruten’s vessels are prepared for maximum utilization of thermal energy by converting heat to power. This technology is currently gaining significance due to new EEXI-regulations and the implementation of the Carbon Intensity Index (CII) energy rating scheme, soaring bunker prices and general environmental awareness in the maritime community.
In Havila Kystruten’s case, the system will generate electricity by surplus thermal energy when all direct consumer systems are served, ensuring maximum energy utilization.
Generating electricity from waste heat can predominantly be done from two fundamentally different processes:
- Organic Rankine Cycle (ORC), and
- Thermoelectric (Peltier-Seebeck effect)
While the ORC process is well-known and already applied in maritime applications, Thermoelectric Power Generation (TEG) is rapidly proving itself as it offers key benefits in terms of payback, operating costs, durability and modularity.
Impact
Havila Kystruten is scheduled to conduct 34 roundtrips between Bergen and Kirkenes along the Norwegian Coast during a year. In a case study analyzing the impact of the automated central heating system, results indicate that 15% of fuel costs can be saved (avoided) during one year of operation. The assumption here is that the alternative is that no heat recovery is installed and heating in done purely by electricity from generator sets.
The economic and environmental impact of this is that each of Havila Kystruten’s 4 vessels will avoid consuming 1120 tons of LNG each year – LNG which would otherwise be consumed to serve the ships heating needs. For the fleet this amounts to 4480 tons of fuel per year, avoiding 10800 tons of CO2 to be emitted into the atmosphere.
From an economical perspective, the payback of the system proved to be less than 10 months.
In summary – exploiting the opportunities which lies in thermal energy management will result in:
- Lower fuel consumption
- Lower emissions of CO2
- Short payback and lower operating expenditures (OPEX)