Short payback and lower operating costs
Investing in equipment and systems for managing your waste heat from combustion processes onboard is probably the lowest hanging fruits available in a newbuild or retrofit project.
The key is to identify consumer systems (mostly electrically powered) where thermal energy could do the same job.
Take heating and cooling as an example: A lot of appliances and systems are typically installed to deliver heat, either to enable a process or for general accommodation heating (HVAC). Instead of powering these with electricity from main or auxiliary switchboards, utilizing waste heat is more economical.
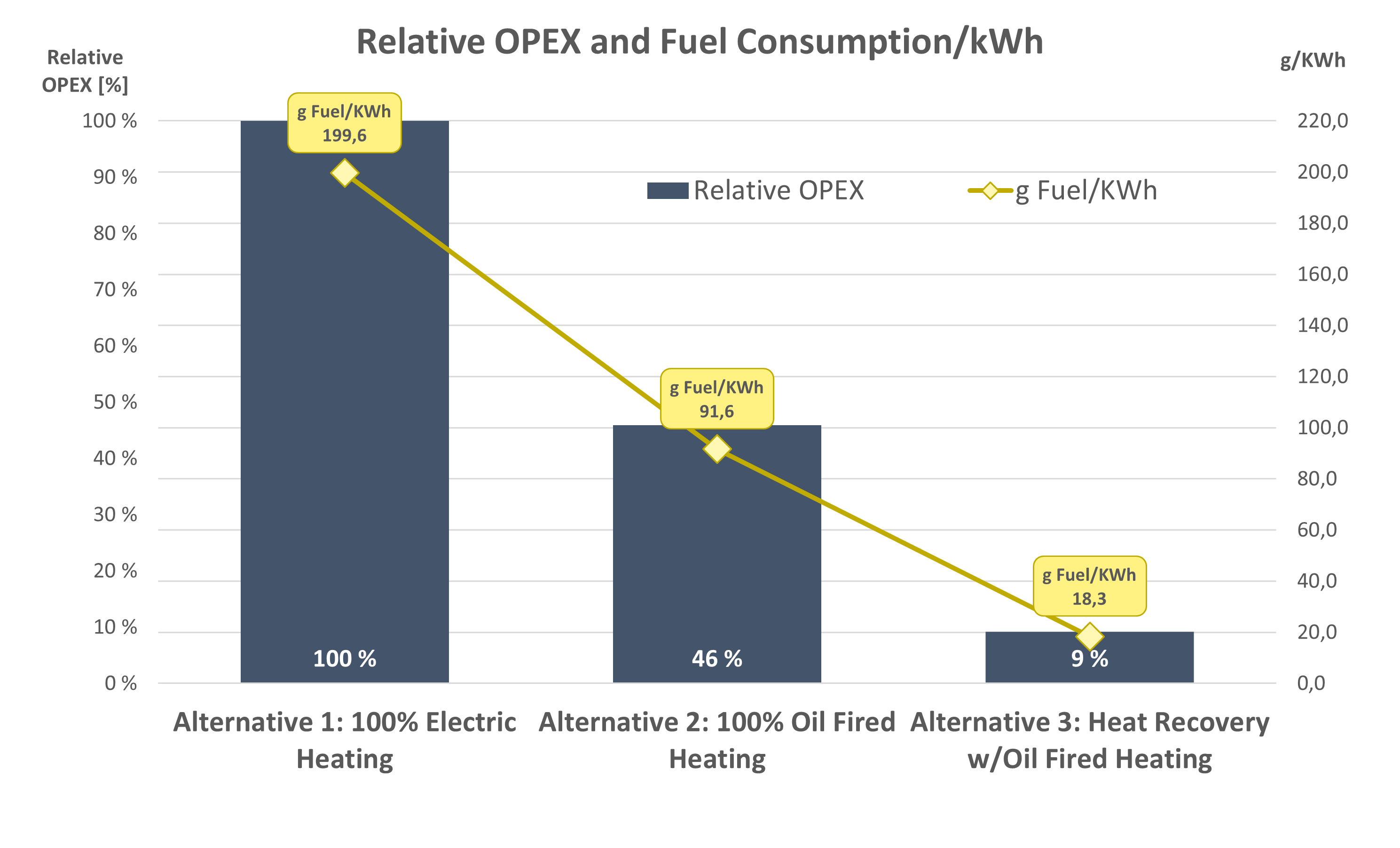
The example below details this:
- Generating electricity will typically require at least 200g fuel per delivered kWh of heat
- The same heat from a fuel fired heater typically requires 92 g/kWh, approximately half the cost
- However, by combining fuel fired heating with heat recovery could in theory eliminate fuel consumption totally!
- ~The example below is from a fishing vessel who managed a heat recovery rate of 80% - the total heating costs ended up being just 9% of the ownerβs previous vessel which was electrically heated.
- ~Converted to fuel, the saving amounted to over 300 tons over an 18-month period!
For every 1 electrical kW rather served with thermal power, 1 ton of fuel* is saved annually
*6000 operating hours/year, 70% average heat load factor, thermal efficiency main engine ~ 44%
With todays technological developments utilization of waste heat has a wider span than just a few years ago. Heat can be used for direct and indirect heating, generating electricity, creating chilled water and treating ballast water.
The more consuming processes identified, the better the business case becomes!
The payback time for Ulmatec's systems are typically between 0,5 and 2 years for reference projects.